Any technology used in the aerospace industry needs to be able to withstand the harshest conditions with minimal risk of fault or failure – lives depend on it. Aerospace PCB manufacturing is a serious business where even the laws of physics are often working against you – thermal management is just one of the many issues you need to work your way around. Aerospace PCB manufacturing requires knowledge of the many ways in which thermal management can impact a component.
Introduction to PCB thermal management in aerospace
Aerospace environments pose unique challenges for PCBs – they’re exposed to radiation, chemicals, pollution, and subject to extreme temperatures that can change rapidly. Many electronic components only work when kept within a specific temperature range – if outside of this range by too far or for too long, you run the risk of parts becoming faulty, or ceasing to work at all. This is why thermal management is so crucial when designing and manufacturing PCBs for aerospace.
Thermal management is not only a safety concern, but also often a regulatory requirement, so it’s an important element to understand. At ABL Circuits we understand the stringent requirements of the aerospace industry, for which we have been manufacturing bespoke PCBs for over 40 years. Here we share some of our wisdom regarding PCB thermal conductivity and what can happen if it’s managed incorrectly.
Understanding the aerospace environment for PCBs
Aerospace is a term that covers flight both inside and outside of the Earth’s atmosphere.
Here is a list of some of the things that aerospace electronics, including PCBs, encounter on a regular basis:
- Extreme temperatures – there are lots of things that can impact the temperature of aerospace electronics, and cause that temperature to change very rapidly e.g. going from the coldness of space to the extreme heat of reentry.
- Vibrations and sudden shocks – launching aircraft involves huge shocks and high vibrations; PCBs must be able to withstand these conditions without taking damage or deteriorating too quickly.
- Exposure to radiation – The radiation experienced in space can cause electronic components to degrade over time, impacting performance and reliability.
- Changes in gravity – Weightlessness can have a huge impact on vital systems, so it’s important it’s accounted for in space-bound craft. For example, cooling systems that use liquid may struggle if the liquid needs to flow in a particular direction.
- Vacuum (airless) conditions – Similar to the lack of gravity, the fact that space is a vacuum can also impact the performance of certain systems e.g. any that need air to dissipate gases or heat.
- Having to go long periods without maintenance – While it is possible to maintain electronics on space stations and some satellites, some probes are designed to be sent into space for extended periods of time. It’s important they’re able to continue functioning even without regular maintenance.
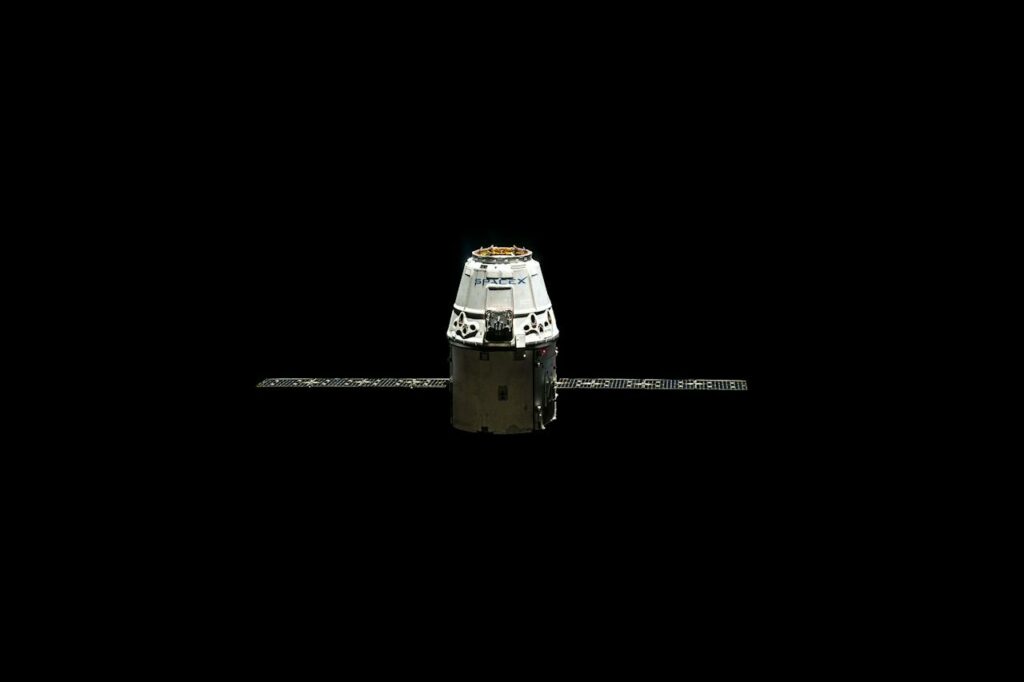
Selecting the right materials
Some materials are better than others when it comes to thermal management. Heavy copper is particularly popular thanks to its enhanced heat dissipation properties. It also has a higher current-carrying ability than regular copper. Adding heavy copper layers to PCBs intended for use in the aerospace industry can increase their structural integrity and thermal stability.
Other materials used in aerospace PCBs include ceramics, teflon-based materials, and epoxy composites. Materials are selected based on their durability, ability for heat dissipation and how easy they are to work with.
Thermal and power distribution analyses
Vital aspects of aerospace engineering, these two types of analysis are carried out to ensure PCBs are optimised. Thermal analysis identifies hotspots and areas of potential improvement to the PCB layout to help with heat management. Power distribution analysis assesses how well electrical power is distributed across the PCB. Both of these processes can help to minimise heat generation, and prevent the components from overheating or losing excessive energy through heat.
Carrying out this analysis is one way of making sure your PCB layouts are optimal and managing heat effectively. Detecting areas in need of improvement will help to prevent problems before they occur, and have a positive impact not only on performance but also the costs associated with the project.
Optimal surface finishes for aerospace PCBs
There are specific finishes and coats that can help to ensure the success of PCBs destined for use in aerospace.
HASL
Hot air solder levelling (HASL) is a finish that involves coating a PCB in molten solder, usually made from tin or lead. It provides an extra layer of protection to your components, but its thickness means it may not be the best option for situations that involve thermal stress.
Gold
The precious metal gold is highly resistant to corrosion and considered relatively malleable, making it an incredibly useful finish to apply to PCBs. Sometimes gold is combined with nickel to make electroless nickel immersion gold (ENIG) – the nickel makes a good barrier against thermal stresses, while the gold protects against oxidisation.
Effective heat dissipation techniques
Here are some examples of techniques used for heat dissipation in the aerospace industry.
- Thermal vias – holes in PCBs that use thermally conductive materials to allow the transfer of heat between layers.
- Liquid cooling systems – a liquid coolant is circulated close to the component creating heat in order to regulate its temperature.
- Cryogenic cooling – the use of cryogenic liquids (such as liquid nitrogen) to rapidly and effectively cool electronic components.
- Heat sinks – devices designed to attract, absorb, and dissipate heat.
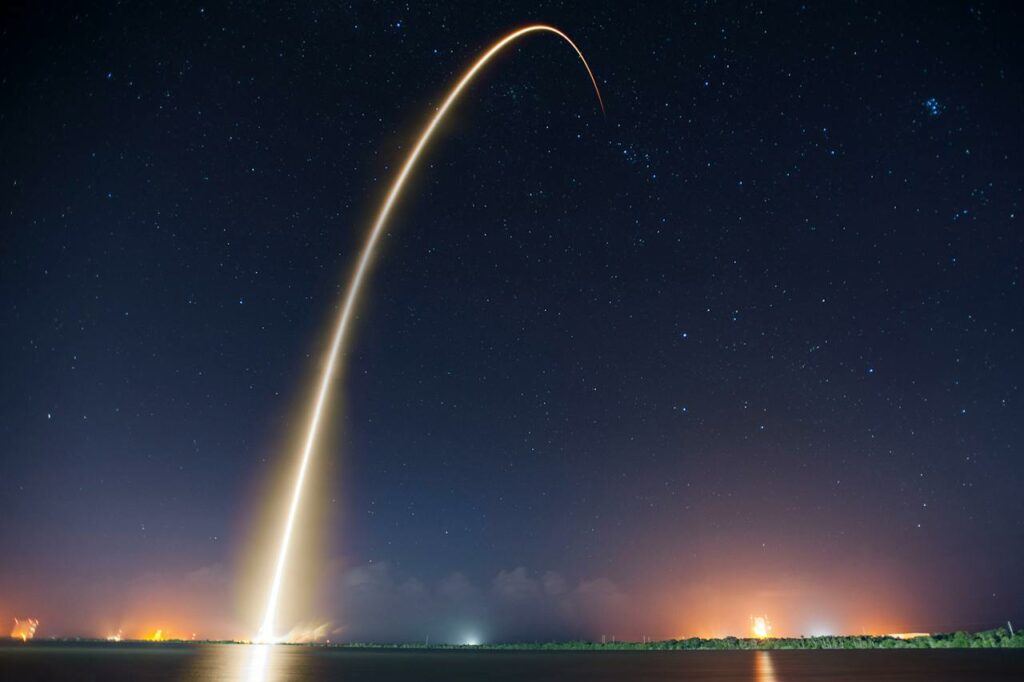
Passive vs active thermal control systems
Heat management systems can be either passive or active. Passive systems utilise the inherent properties of the materials used, whereas active systems rely on active mechanical components, such as fans or pumps. In most cases a combined approach of both passive and active techniques is used in order to achieve optimal results.
Importance of component placement
Component placement can have a big impact on thermal management. Proximity to heat sources, allowing for natural ventilation and airflow, and keeping temperatures uniform can all contribute towards effective thermal management. Prototyping and thorough testing will aid in making sure components are positioned as effectively as possible.
Compliance with aerospace standards
Thermal management falls under many of the universal quality management standards and safety regulations of the aerospace industry. These standards apply to everything from the supply chain of materials to requirements for documentation and record-keeping.
For example, many aerospace systems are subject to specific temperature ranges. These ranges are industry standards, and are often decided based on what is safe and efficient. A system that runs too hot might be a danger, whereas one that runs too cold might not be able to work to its full potential.
Running simulated scenarios and conducting thermal analysis is an important part of the aerospace PCB design and manufacturing process – without these tests, you cannot ensure that your components will work to regulation when in use. Engineers and designers must be well-versed in industry standards to keep their work compliant and achieve the appropriate certification.
Ensuring aerospace PCB reliability
Thermal management needs to be a key consideration throughout the entire PCB manufacturing process, and can have dire consequences if overlooked. Put our skills to the test and see how ABL Circuits can help you with aerospace PCB design solutions. Get a quote today.