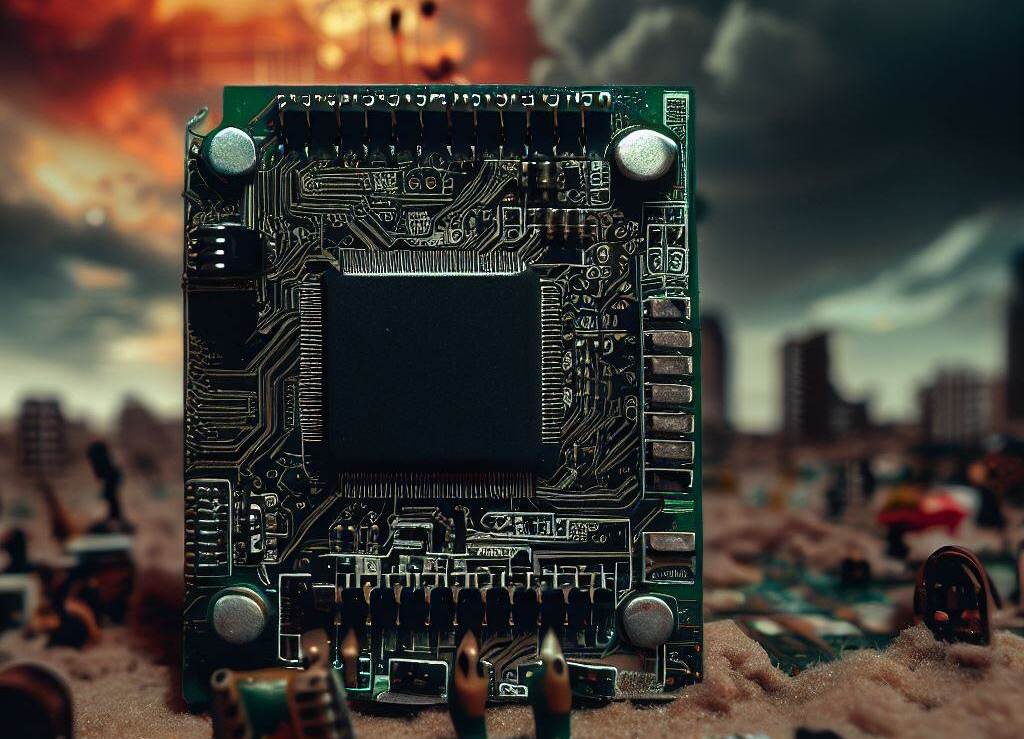
Bringing your desired product to life can be a time consuming process. A lot of thought, planning, and resource goes into making sure your dream can become a reality with your design. Consequently, it is extremely important to ensure you have designed a PCB that can stand the test of time, have a long shelf life and remain competitive within the market, so all your hard work has not gone to waste. There are a number of factors that can affect the shelf life of your PCB, this blog will explore these various aspects and how ABL Circuits can help manage this process.
What factors can affect a PCB lifespan?
A number of factors can affect the lifespan of a PCB, none less than the environment it is operating in, as some PCBs may be built for devices that need to withstand extreme environments, such as high temperatures. Whilst PCBs are accurately designed so they are fit for their purpose, it goes without saying that everything has an expiry date, and having transistors exposed to certain conditions for a long period of time can result in PCBs burning out.
Component quality
One of the main factors which could affect the lifespan of your PCB, is the quality of components. Sourcing components from a reliable source and ensuring they are properly soldered, and tested, is important to ensure they can stand the test of time. Left over flux can also be a big problem affecting the quality of components. Flux is a chemical cleaning agent used in the soldering process, they are used to remove any impurities from the surface of the circuit board. However, if excess is left on the board, this can lead to corrosion and thus a quick deterioration of the board.
Vibration
Some PCBs may be used in devices, such as construction equipment, where they need to withstand high vibrations. Whilst they will be carefully manufactured for this purpose, vibrations, regardless of the PCB, can still cause damage over a sustained period of time. This is due to the vibrations causing the PCB to bend, this can damage, or even break, components and soldering, due to them bending and ultimately snapping which can lead to complete failure of the board.
Thermal shock
Thermal shock can occur during the manufacturing of a PCB when a board is heating to a high temperature in a short period of time. This causes extreme pressure on the board and can lead to it expanding or contracting, a similar reaction can also happen if the board becomes too cold. The board expanding or contracting can lead to components breaking and ultimately the board failing. That being said, not all the effects of thermal shock are visible, for example, thermal shock can result in trapped moisture, which can be another issue for the board, which we will come to shortly.
Manufacturing quality
Whilst there are a number of tests manufacturers follow, such as thermal shock testing, to ensure the board has been manufactured to the highest quality for a long shelf life, errors can still occur within the board. Some of the manufacturing issues could include leftover flux on the board, poor solderability, or lack of, which can all affect the quality of components and functioning of the board. Other manufacturing issues which can affect the lifespan of a board are low quality substrate materials, which can affect the electrical signals within the board and thus its performance. Additionally, misaligned layers in a PCB board.
Moisture
Moisture can become trapped within the glass of a PCB, such as in the epoxy glass or within any of the glass interfaces. Moisture can also have a detrimental effect on the functioning of a PCB by reducing the quality of lamination, or damaging the solder mask, both important factors in the assembly manufacturing and assembly process. This can lead to the board running at slower circuit speeds and can lead to complete failure of the board. A process called pre-baking can be used to try and avoid moisture becoming trapped and thus protecting it to provide a long shelf life. .
User interaction
When manufacturing and assembling a PCB, manufacturers will ensure they are doing all the necessary tests, and carrying out all the precautions they can to ensure your board has as long a shelf life as possible. However, ultimately the lifespan of a PCB will also come down to the user interaction of the product as an end result. If the board is being used within a product that is being used daily and constantly being handled, ultimately the lifespan of the board will be less than the board of a PCB used less frequently. For example, take your iphone, or smartphone charger, it’s likely that you use this everyday, or every night, to charge your phone. The board within your smartphone charger is likely to have a lower life span compared to the board within a product you are not handling and using daily.
PCB – life cycle analysis
Why it’s important
The PCB life cycle analysis looks at the environmental impact of PCBs, from the fabrication of the board through to the manufacturing process. The analysis is important in order to inform and educate manufacturers on how they can help minimise the environmental impact of PCB production. PCBs produce a high volume of freshwater aquatic ecotoxicity potential and ozone layer depletion potential.
PCBs have a long life cycle, with various processes and steps needing to be undertaken to create a high quality board for desired end products, from etching to solder masking, all the way through to testing, this can require a lot of energy and resources. Therefore, it is important for manufacturers to ensure they are being as environmentally friendly as they can be with their materials and processes.
How do we manage this process?
There are several ways a manufacturer can help to reduce their carbon footprint and help the environment, where possible. The first of these is cutting down on the use of lead solder, and instead opting for lead free solder within the soldering process. At ABL Circuits we always ensure we are using lead free solder, as not only does it have a lower melting point and therefore more energy efficient, lead free solder also does not contain the same harmful chemicals as lead solder, and is therefore much better for the environment as a whole. Additionally, at ABL Circuits, as well as creating new PCBs for products, we also offer a service to rework older PCBs. Meaning, if you come to us with a request for a board, we will always check if there is an older board you already have that we can rework and fix, instead of making a new board from scratch, to help recycle products and reduce our carbon footprint.
It is also important to ensure you are recycling your materials where you can, such as metal, fibreglass, solid and liquid waste, something ABL Circuits work hard to do.
Designing the best PCB for your needs
At the ABL Circuits we offer the full start to end service for all your PCB needs, from design all the way through to manufacturing and assembly. This means we can work with you to design in the PCB you require for your product. In other words, when we work with customers we will decipher how long you would expect, or need, the board to last within your final product. Of course, the answer here may likely be ‘as long as possible’, however, if your board is being used in a military product or for aerospace, for example, it will need the longest shelf life possible. We will therefore ensure that the highest quality components are being used and testing is extremely thorough throughout the entire process. Depending on how long a product is needed for, we may use different components that are the most appropriate for the end result and the desire life span.
Need expert support on PCB design or manufacture?
If you’d like to find out more about how we work and how we can help you, get in touch for a free quote.
If you’d prefer to arrange discussion with a member of our team, then you can reach us via the contact page.