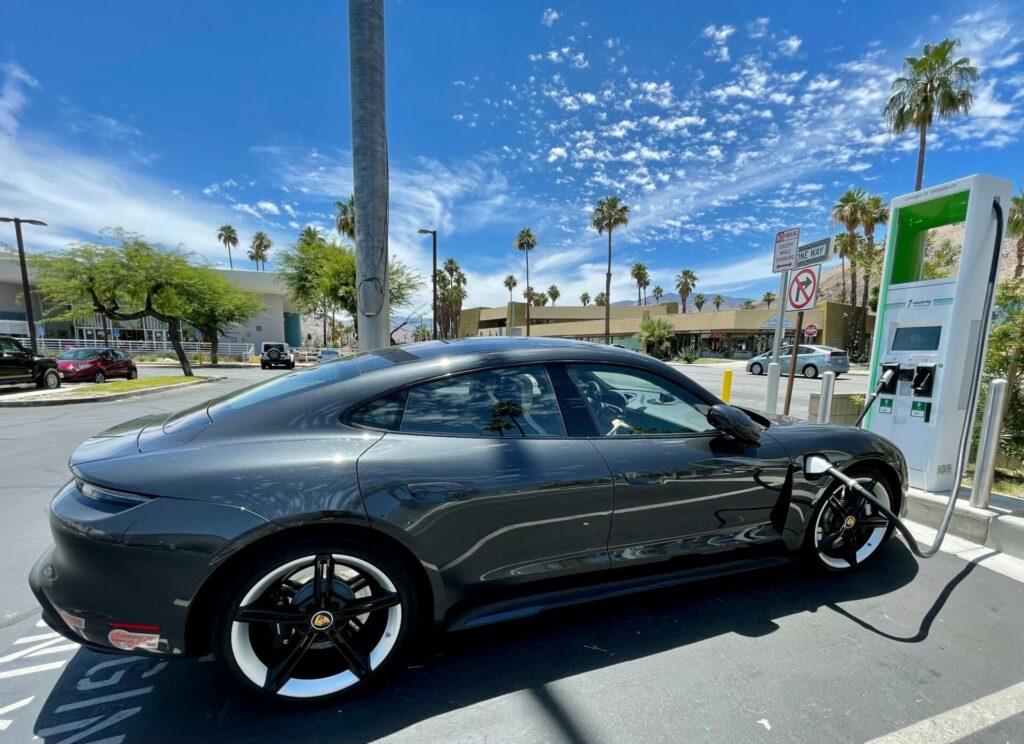
There’s no denying that electric vehicles are the future of motoring, despite the recent talk of delaying the switch. As the country continues to prepare for the phasing out of petrol and diesel vehicles the focus turns to making EVs as efficient and appealing as possible, to make the transition easier on people who may still have reservations about the eco-friendly alternatives to fossil-fuelled cars.
As with many modern electronics, including traditional internal combustion engine (ICE) vehicles, printed circuit boards (PCBs) are a key component in EVs. There are hundreds of circuit boards in cars – they are found throughout the electronic systems that keep them running, and their reliability and durability are essential to making EVs a viable alternative to ICE vehicles.
Where can you find PCBs in electric vehicles?
PCBs can be found throughout EVs, as they are used to connect various electronic components. The key areas in which they are used include:
- Control units for heating and air conditioning
- Anti-lock braking systems
- Delivering power to the electric motor
- Managing individual cells within the battery pack
- Infotainment systems
- Charging and power distribution
- And many more
The benefits of using PCBs in electric vehicle components
The PCBs used in EVs face unique challenges, due to the way in which EVs are made and how they run. They must be able to handle high-voltage systems, rapid charging, temperature changes, and the general wear and tear that comes with being on the road. Here are some of the benefits of using high-quality PCBs in EVs.
Compact and lightweight
Weight is an important factor when it comes to EVs. The overall weight of the vehicle can have a significant impact on the battery life and the distance it can travel between charges. The battery packs required to run EVs are big and extremely heavy, sometimes making up the weight of a regular car on its own. With this in mind, the goal in making EVs is always to pack more energy into less mass wherever possible.
While they can vary significantly in their construction, PCBs are always designed to be lightweight and compact while still meeting the requirements of the systems they’re built for. They are often made from light, electrically-insulating materials, chosen with the end product in mind – in this case, PCBs for EVs are created with the weight issue at the forefront of the design process.
Durable
All of the components for automobiles need to highly durable, due to the nature of the conditions they encounter on the road:
- Vibration and shock resistance are of particular importance, even in EVs that aren’t intended to go off-road. The robust materials and secure soldering used to construct EVs make them incredibly durable.
- Temperature tolerance is also very important, as many of the components within an EV generate a lot of heat. Not only are PCBs designed to operate within wide temperature ranges, they are also often equipped with their own thermal management features.
- EVs manufacturers tend to promise a minimum lifespan of 10 years from their vehicles, though many will reliably outlive this. The PCBs within them must have equal longevity and are designed with this in mind.
Efficient operation
PCBs contribute to the precise control, monitoring and optimisation of various internal EV systems, helping to maximise their energy efficiency. One of the best examples of the efficiency of EVs is their regenerative braking, where kinetic energy is captured during braking and sent back to the battery – this process would be impossible without PCBs controlling and monitoring the transfer of power, with minimal energy waste.
Many of the areas in which PCBs contribute to the efficient operations within an EV are in relation to energy management. They’re used in Battery Management Systems (BMS), which monitor the health of battery cells; they’re also essential to any power electronics, optimising the flow of electricity to different vehicle subsystems.
Crucially, they keep the EV charging process as efficient as possible. Charging anxiety is the main concern for EV drivers, with worries about finding a charge point before the battery dies proving to be more pressing than range anxiety. EVs charging quickly and efficiently is key to encouraging more people to go electric, so the PCBs involved in charging control serve an incredibly important purpose.
How long will a PCB last?
As mentioned when discussing the durability of PCBs, a PCB needs to be able to outlast whatever machinery it is built into. A number of factors can impact the lifespan of a PCB, including:
- The quality of the materials used.
- The stress it comes under during day-to-day use.
- Whether or not it requires maintenance.
- The lifespan of individual components within the PCB.
On average, you can expect a well-made PCB to last anywhere from 15-20 years, potentially more. This is one of the reasons why it’s important to use PCBs that have been built to last.
How will electric cars impact the PCB industry?
As the demand for EVs rises, so too will the need for reliable PCBs. The number of people buying EVs is already rising at a rapid rate, and when the ban on producing new ICE vehicles comes into place we can only expect this number to increase exponentially. The global PCB market is estimated to hit at least $13.39 billion by 2030, and the production of EVs will undoubtedly contribute to this number.
EVs need PCBs that can be compact, handle clean energy conversion, and support the IoT, and these demands will continue to push PCB manufacturers to compete with each other, hopefully producing great technological advancements in doing so.
Conclusion
PCBs in cars, both electric and ICE, are essential components. When seeking a bespoke PCB solution, you want a manufacturer with experience in the industry that can take you through all stages of the process. To find out more about ABL’s automotive expertise, including case studies of our successful solutions, visit our automotive page and get in touch via the form.