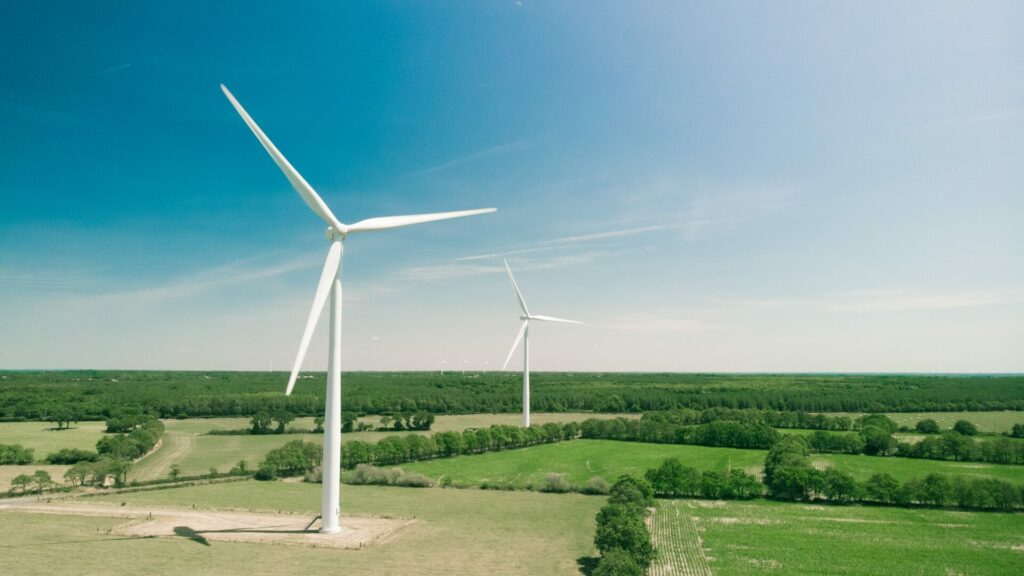
The relevance and significance of offshore wind turbines continues to grow in the ongoing fight against environmental and economic energy challenges. Recent international security concerns have accelerated the need for reliable transitions to clean energy, and wind farms will no doubt play a significant role in the discussions and developments to come.
The concept of wind power is fairly simple, but the thought that goes into designing and manufacturing the machinery that makes it possible is not. Printed circuit boards (PCBs) are used in many wind energy components, and need to be up to the task of enabling and supporting this important work. Here we will share some of our knowledge surrounding clean energy PCB applications, including the features that PCBs used in offshore wind turbines need to possess, and why.
How does a wind turbine work?
Wind turbines use wind to generate energy. When wind causes the blades of a turbine to rotate, the kinetic energy creates electricity with the help of a rotor and generator. We’ve been using wind power for as long as boats have had sails, and in wind-powered pumps and windmills.
Wind turbines take this concept and blow up the proportions, literally. The average onshore wind turbine is between 240-280 feet tall. Offshore wind turbines are even taller, built to absorb the powerful winds that blow at sea, and can be over 600 feet high. When grouped together, turbines form wind farms, and provide an alternative to traditional power stations. Building these farms offshore helps to avoid conflict caused by the space they would take up on land.
Wind is an unlimited power source, and a green alternative to methods that involve burning fossil fuels, such as coal and oil. Using green energy sources to create renewable energy systems is vital to reducing carbon emissions. For this reason, it’s important that wind turbines are built and maintained effectively, so they can be a viable option as a main source of energy for the future.
Key considerations when customising a wind turbine PCB
There are many things to consider when building PCBs for wind turbines.
Size
As mentioned above, offshore wind turbines are simply huge. However, the free space inside their mechanisms is surprisingly limited. PCBs must be built with this in mind, to ensure that they can be built into wind turbines without compromising functionality.
Material
Salty air and saltwater are known for their corrosiveness. PCBs for offshore wind turbines must be made as corrosion-resistant as possible. One of the best methods to do this is to conformal coat the PCBA as well as seal them in water and corrosive resistant enclosures. , specifically those designed for marine use. This prevents the components and materials from breaking down over time while exposed to the elements. Offshore wind turbines need to be built to withstand the storms and high winds at sea. The rough and hostile nature of the environment means the PCBAs will experience high vibrations throughout it’s lifecycle. This can potentially damage solder joints over time and stop the unit from working.
Reliability
Wind farms are created with the expectation that they should be able to run for a minimum of 25 years. While they’re regularly serviced and maintained by dedicated crews of turbine technicians, the less attention they need, the less time these crews need to spend at sea. There is also the fact that turbines can pose a safety risk to those who work on and around them, and in their immediate surroundings, if emergency shutdown systems are not working properly. The reliability of the PCBs within these emergency systems is incredibly important.
Challenges of customising a wind turbine PCB
As well as the elements, PCBs in wind turbines face a number of technological challenges, and have many specific tasks required of them.
Maintaining integrity
In terms of integrity we’re referring not only to the physical integrity of the PCBs, but their ability to carry out the jobs they are made for and allow the wind turbine to work to its fullest potential. There are many sensitive electronic components within wind turbines that may be susceptible to electromagnetic interference. PCBs for wind turbines must be designed to minimise as much interference as possible, and enable accurate data transmission from the turbine back to land.
Power
Offshore wind turbines operate at high voltages and currents. A single wind turbine can produce more than 6 million kWh of electricity a year – enough to power thousands of homes. Wind turbine PCBs must be able to distribute power efficiently with minimal loss, and safely manage these high power levels.
Sustainable materials
The point of wind farms is that they are a green energy source, so it is only right that wind turbines and their components should be made as sustainably as possible. This has an effect on all areas of PCB production, from using recyclable (but still durable and safe) materials wherever possible, to reducing the involvement of harmful materials and hazardous substances. It’s important that manufacturing is as efficient as possible to minimise the carbon footprint associated with production.
Conclusion
When it comes to energy, there are many applications for well-made and reliable PCBs. Energy will continue to be a hot topic, as advancements are made towards making clean, green energy a more imminent reality. More and more the focus will be on creating PCBs that are able to meet the following criteria:
- Capable of handling harsh environments
- Made from sustainable materials, without compromising reliability
- Widely customisable, to suit a variety of purposes
If you’re looking for bespoke PCB solutions, we have a wealth of experience at our disposal and are eager to help. Get a free trial today and enhance your product with ABL Circuits.